Advantages of Sandblasting Booths, and their Components
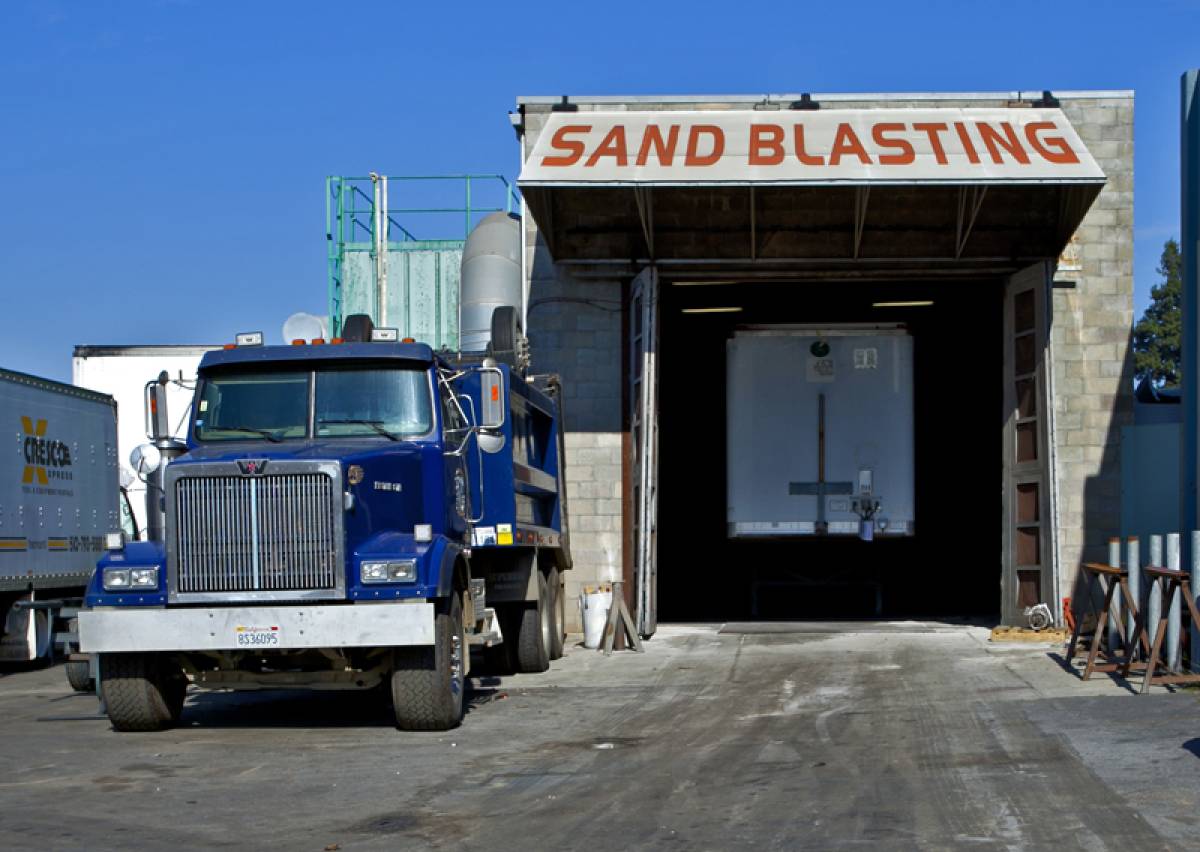
Sandblasting is a process in which minute spherical or angular particles of abrasive materials are pushed at high speeds using compressed air.
Industries use abrasive blasting for various purposes, including cleaning, smoothening, shaping, and eliminating rusting on surfaces.
The machinery used for this purpose is a sand blasting booth or abrasive blast room. It delivers, reclaims, and contains the media, preventing it from escaping outside.
The booth contains the materials used in the blasting process and then collects the dust once the process is complete.
The blast processing capability depends on various factors like the media’s type, shape, size, density, hardness, volume, acceleration capacity, impact angle, and time cycle.
Blast rooms with pneumatic or mechanical recovery systems offer the most efficient and safest sandblasting environment, enabling you to operate irrespective of outside weather conditions or the size of the materials used in the blasting process.
But what are the advantages of these booths? What are their key components, and what other details should you know about them?
Advantages of Abrasive Blasting Booths
The best booths have dust collections that adapt to a room’s size, consist of floor hoppers, and an abrasive recovery system with a recovery rate of more than 95%.
Here are some other advantages.
Higher visibility
The presence of high-efficiency LED lights, with the Hi-Bay 18,000 lumens lighting system, provides complete visibility of the blaster inside the booth.
The efficient design allows one person to install, clean up and replace the lights inside the booth.
It removes the need to climb on the roof for maintenance or incur the costs of hiring additional personnel to service or clean the lighting.
Extremely strong
The heavy-duty blast booths are made from industrial-grade modular 14-gauge galvanized or powder-coated finish steel panels.
Structural beams supporting the walls and roof make the enclosure capable of withstanding the enormous weight of lifting equipment without incurring any damage. You can also opt for higher industrial steel gauges for larger rooms.
Preventive maintenance program
A preventive maintenance program (PMP) ensures that the machinery remains in optimal working condition for at least two years after its installation.
That is made possible by a Programmable Logic Controller (PLC), interfaced with a Human Machine Interface (HMI) touch panel, which automates the operations of critical components.
The maintenance program, integrated into the booth’s system, sends a reminder when it’s time to run a maintenance routine on the components or perform a quality check.
Code Compliance
The components meet the standards determined by the Occupational Safety and Health Administration (OSHA).
At the same time, explosion-proof dust collection systems comply with the standards set by the National Fire Protection Association (NFPA).
For example, emergency stop and safety features like safety door switches and stop devices protect workers during blasting, while Grade D breathing air ensures optimal respiratory protection.
Main Components of Blast Booths
Booth enclosure
It is the central part of the machinery where the blasting operations occur. A modular designed enclosure contains various personal door and product entry door configurations, allowing the smooth entry of both operators and products.
The enclosure contains one standard access door and optional bifold or trifold access doors when space is a problem. You can also opt for a rubber roll-up door system for limited space installations or quick opening and closing doors.
Media recovery system
Media refers to the product used in the blasting process and is of two types: angular-shaped and spherical-shaped. You can choose between pneumatic and mechanical recovery systems to recover the leftover media on the floor after the blasting operation.
The recovery system filters out the dust and foreign particles and transfers them to the dust collector, leaving you with clean, workable media. It is cost-effective (as you don’t have to buy new media for every blasting operation) and beneficial to the environment (as it reduces abrasive media consumption).
Dust collection and filtration system
Reverse pulse cartridge dust collectors can collect about 99.9% of particles with an automated cleaning process to increase the cartridge media’s longevity. A single unit contains between six and 24 cartridges and delivers up to 50,000 CFM.
Pressure blasters and storage hoppers
Pressure blasters supply up to four blasters at once and are operable from inside the booth to increase productivity. The blast pots have a tank capacity of between 3.5 and 10 cubic feet.
Long uninterrupted hours of blasting are made possible by storage hoppers installed between the media separator and blast pot.
In Conclusion
A sand blasting booth with a pneumatic or mechanical recovery system has a lot of advantages, from increased visibility to excellent recovery rates.
It offers the ideal environment for efficient sandblasting operations to clean an object or surface, remove burrs, apply a texture, or prepare a surface for the application of paint or other type of coating, while ensuring compatibility with popular media such as aluminum oxide, steel shot, glass beads, GMA garnet, and steel grit.