The Art & Process Of Manufacturing Personalized Stubby Holders
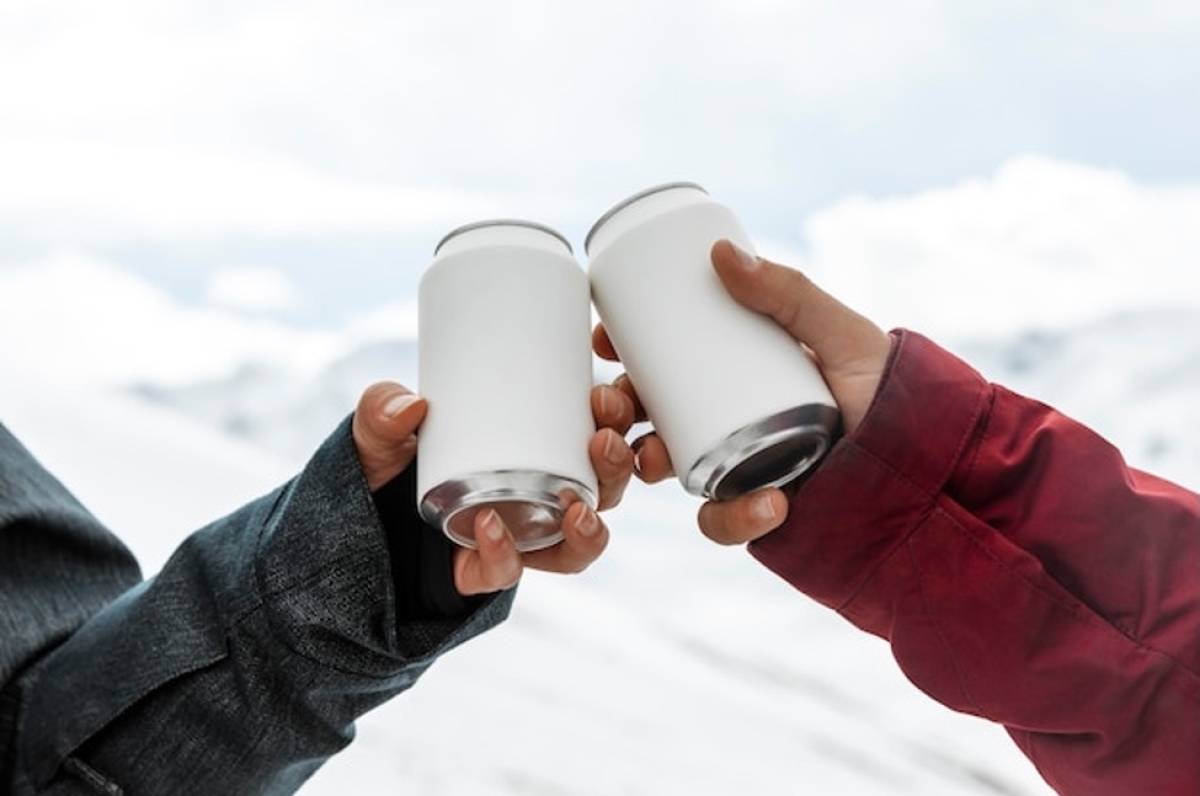
In the world of promotional items and personalized mementos, stubby holders occupy a special place. These handy accessories, designed to keep beverage containers cool and comfortable to hold, offer a functional canvas for personal expression and brand promotion.
The process of transforming a simple stubby holder into a personalized token involves an intricate journey from design conception to final production.
In this article, we present a quick exploration of the manufacturing process of personalized stubby holders, revealing the art and science behind these ubiquitous accessories.
Let’s begin...
Steps for Creating Personalized Stubby Holders
Customized Cunnamulla stubby holder.
1. Client Consultation and Design Creation
The journey of creating a personalised stubby holder begins with understanding the client's requirements. Whether it's a company logo, a witty quote, or a custom design, the client's vision forms the backbone of the personalisation process.
Designers collaborate with clients, considering the color preferences, text inputs, and graphics involved. Advanced software tools are then utilized to transform these ideas into a viable design ready for the next stage.
2. Material Selection
Stubby holders are typically made from insulating materials, such as neoprene, a synthetic rubber known for its excellent temperature regulation properties.
The thickness and quality of the material chosen have a significant impact on the holder's performance and longevity.
Personalization needs, such as the design's complexity and the intended printing method, also play a role in selecting a suitable material.
3. Cutting the Material
Once the material is selected, it's cut into the appropriate shape and size. Cutting can be done manually for small-scale orders or using automated cutting machines for larger quantities.
Precision is crucial in this step to ensure the stubby holders will fit the beverage containers securely and maintain their shape over time.
4. Printing the Design
After the stubby holders have been cut out, it's time to bring the client's vision to life. Several printing techniques can be used, depending on the complexity and color requirements of the design.
Screen printing is commonly used for simpler designs with one or two colors. Meanwhile, digital or dye-sublimation printing can handle intricate designs and a broader color spectrum, making them ideal for photographs or detailed logos.
This process must be performed with care to ensure the design is sharp, vibrant, and durable.
5. Stitching the Stubby Holder
After printing, the stubby holders are stitched together to create the final product. This involves sewing the two sides of the cut-out material, forming a cylindrical shape.
The bottom is then sewn on, creating a snug pocket for the beverage container. This task uses Industrial sewing machines to ensure solid and neat seams.
6. Quality Control and Packaging
The final stage of the manufacturing process is quality control. Each personalised stubby holder is examined for material, print, and construction defects. Those that meet the quality standards are then packed and prepared for delivery.
Packaging serves a dual purpose. It protects the stubby holders during transit and presents them attractively upon receipt by the client.
Conclusion
Creating personalised stubby holders entails creative vision, material expertise, technical precision, and attention to detail.
Every step of the process, from the initial design consultation to the final quality control is crucial in transforming a simple insulating material into a vibrant, personalised accessory.
Whether you are promoting a brand, celebrating an event, or just expressing a personal sentiment with stubby holders, these customised treasures testify to the power of personalisation.
The manufacturing process of stubby holders is a testament to the meticulous craftsmanship that goes into creating items that are not just functional, but also meaningful and unique.