Selecting the Best Waterjet Cutting Equipment & Tools: What to Know
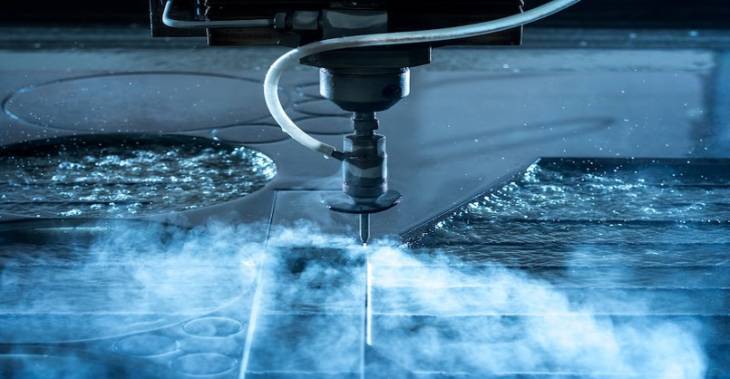
Waterjet cutting is an erosive procedure that employs high-pressure water to cut through various materials to make 2D structures, like foam and rubber gaskets, as well as to cut items like meals and fabrics.
A water jet cutter, when combined with an abrasive, is used to cut hard materials such as steel, aluminum, laminated glass, stone, ceramic, and so on. The machines can replace other processes, such as EDM (another erosive process), plasma or laser cutting, and classic techniques such as milling.
Waterjet cutting has a significant benefit over other processes because it adds no heat to the material during the process, reducing the requirement for post-cutting heat treatment. This makes it particularly helpful for airplane components.
Waterjet Cutting Fundamentals
A computer-controlled X-Y traversing system is used in most waterjet systems to move the waterjet nozzle over the workpiece following CNC (Computer Numerical Control) instructions. An articulating arm can be connected to the head to allow for bevel cuts.
Fixed heads can also be used for slitting processes in which the workpiece moves. To reduce noise and mess, the workpiece is frequently immersed in a water pool. Some systems combine water and abrasive cutting (for hard materials) as well as water-only devices (for soft goods). A jeweled orifice lowers nozzle wear during abrasive cutting.
Waterjet cutting can generate high-quality cuts with inch tolerances as low as a half-thousandth. Stainless steel thicknesses of up to 10 in. are said to be cuttable. The presence of high-pressure pumps, either hydraulic intensifiers or motor-driven triplex pumps, capable of delivering pressures in the 60,000 psi range, is essential for water jet cutting.
Abrasives with round or sharp edges are often used for hard materials, and they are combined with the water jet via a venturi. During a two-hour cutting session, a typical system will use approximately 100 lb. of abrasive.
Waterjet Cutting Operation
Waterjet cutting CNC programming is said to be simple, and many manufacturers offer systems that feed CAD files into production software, which generates G-code for the cutter. Feed rates are created automatically for a wide range of conventional materials and thicknesses.
Although most systems rely on X-Y motion and vertical waterjet nozzle change, 5-axis systems are available.
Waterjet Cutting Process Optimization Equipment and Tools
The correct equipment and tool type and size for a waterjet cutting process can make a substantial difference in the machine’s performance and profitability.
The following are some tools used in the waterjet cutting process:
i. Pump
Water is pressurized to extremely high pressures, over 50,000 psi, by the intensifier-style pump.
ii. Tank
Your waterjet cutting machine’s foundation is the water-filled tank. After the stream has sliced through the material on the table, it discharges its energy.
iii. Cutter Heads
The high-pressure water is routed via a network of stainless steel tubes before being combined with abrasive and driven through the cutting head.
iv. Mini Abrasive Hopper
The tiny hopper delivers abrasive to the nozzle at precise feed rates ideal for cutting.
v. Surface for Cutting
Multiple support provides a flat, sturdy platform for clamping material, which is critical for accurate parts.
vi. Gantry
The bridge-style gantry is automated in the X and Y axes to precisely regulate cutting head movement.
vii. Hopper for Abrasive Bulk Feed
The bulk feed hopper stores hundreds or thousands of pounds of garnet abrasive material, which is fed into the Z-micro carriage’s hopper.
viii. Supervisor
To run the waterjet, the PC-based touchscreen controller (HMI) software translates CAD/CAM files into simple G&M code.
Advantages of Waterjet Cutting
Waterjet cutting is best described as a controlled sped-up erosion process. As a result, the waterjet can cut or erode almost any material, making it one of the most versatile tools available.
Waterjet cutting, as one of the fastest growing machine tool sectors, has been shown to save time and money on a wide range of applications.
Here’s why so many people have chosen waterjet for the benefits it provides:
1. High Accuracy (Tight Tolerances)
Tolerances of less than +/- 0.005′′ are possible, especially in thinner materials such as 1′′ stainless steel.
Waterjet cutting can also adjust tolerances in different areas of a product, assuring the optimum price and quality.
2. Materials up to 12" thick can be cut
Waterjet can cut materials ranging from 0.010′′ acrylics to 10" thick stainless steel, making it an extremely versatile tool.
Even thin materials can be stacked to boost productivity and reduce expenses!
3. Zone Unaffected by Heat (HAZ)
Waterjet cutting is a natural eroding procedure that does not need chemicals or heat. As a result, warping and distortion common in laser, plasma, and oxy-fuel cutting are removed, reducing the need for additional processing.
4. Reduced Material Waste
The width of the material removed during the cutting operation is referred to as the kerf. Kerf sizes for waterjet cutting range from 0.020′′ to 0.050.′′ As a general rule, the less kerf there is, the more precise the cutting tool.
Waterjet kerf is quite thin compared to other cutting methods, which means you may utilize your material to generate the most pieces with the least waste.
5. Common Line Cutting and Nesting
Waterjet cutting, unlike laser, plasma, or oxy-fuel cutting, lends itself to common line cutting. Optional cutting software from Techni Water Jet allows you to nest many forms together and cut them with multiple heads.
You can save costly material by tracking sheet leftovers and nesting your pieces onto these unusual shapes afterward.
6. Excellent Edge Finish
Taper and edge finish is closely related to cut speed and can be tailored to the project at hand. Higher cutting rates produce taper and a coarser edge finish.
The taper can be reduced or eliminated by slowing down the water jet and achieving a high-grade edge finish.
7. Any Industry Can Use Waterjet
The waterjet’s versatility allows it to be employed in practically every industry. Because a waterjet is so much shorter, it may be easier to list the materials that it cannot cut!
In Conclusion
Waterjet cutting is a common machining technology for a wide range of applications because of its precision. Improving waterjet cutting accuracy is critical for consistently manufacturing high-quality products. Take time to select the best equipment and tools that match your high tolerance needs and solve your most complicated cutting challenges.