The Basics of Abrasive Blasting You Should Know
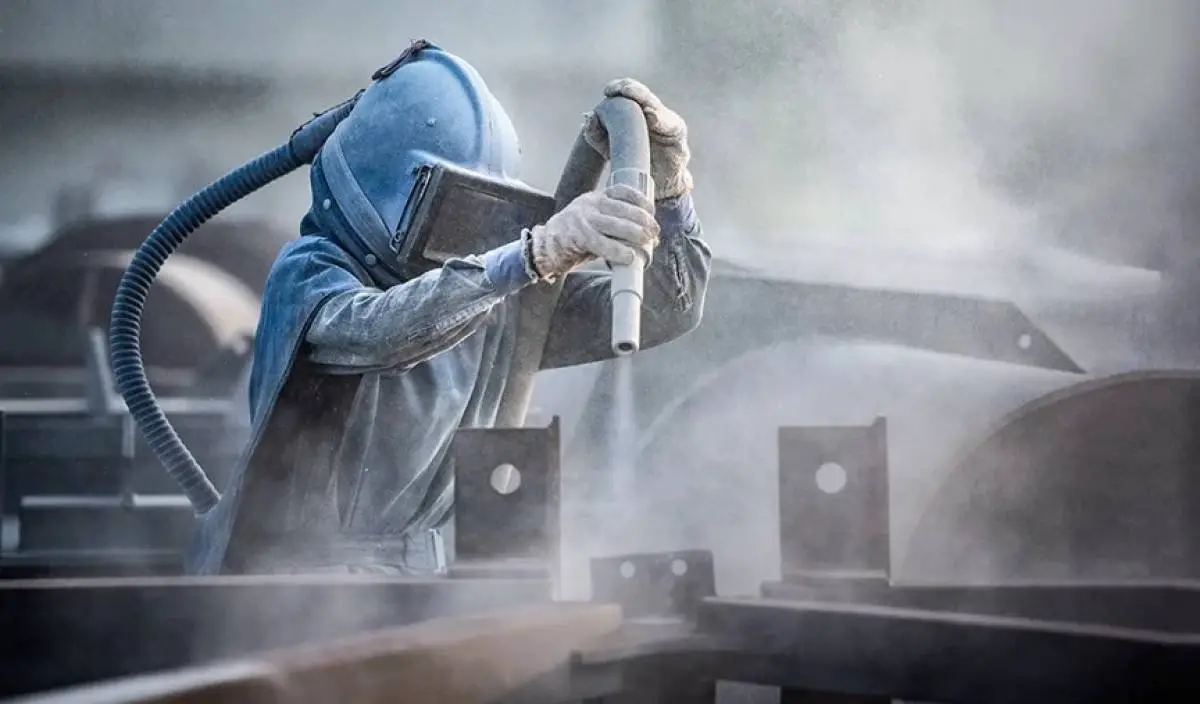
Abrasive blasting operator at work. Photo: N_Sakarin / Shutterstock
Grit blasting, media blasting, or sandblasting are processes that are more commonly known as abrasive blasting. All of these processes refer to abrasive methods of cleaning and preparing of surfaces such as steel for painting or other purposes.
In abrasive blasting, a stream of compressed air and sand-sized abrasive material is propelled at high velocity against a surface under high pressure to smoothen a rough surface, roughen a smooth surface, clean a surface, or remove surface contaminants.
This method of modification and preparation of surfaces to make them smooth, clear, or finished can differ based on the type of blasting material used. You can use different abrasive blasting materials depending on your specific modification needs.
For example, you may require a different type of abrasive material in cases where surface dust and containment are significant concerns for you. Each of the different abrasive materials available caters to specific needs you may have, and will usually require the use of varied kinds of abrasive blasting equipment.
How Abrasive Blasting Works
In abrasive blasting, three key components are usually required to get the job done:
- The blasting pot or the blasting cabinet
- An air compressor to compress air and force the abrasive mixture out at high pressure, and
- A blasting gun to control the abrasive blast itself that is applied directly on the surface being prepared.
In addition, there are controlled environments like a blasting cabinet or a blasting room you can use to safely carry out abrasive blasting, especially for large power projects.
Similarly, various abrasive blasting equipment, machines, or pressure pots are available for different projects. Before you choose your abrasive blasting equipment, you’ll want to first understand the different types of abrasive blasting that can be carried out to achieve specific results, so that you can choose the right equipment for the job.
Type Of Abrasive Blasting
Sandblasting Booth. Photo. BEAR RV/Wikipedia.
I. Shot blasting
Here round or stainless steel shots are propelled onto the surface at high velocity from a mechanical device that employs centrifugal force.
This type of blasting is ideal for quick cleaning surfaces, removing contamination on metal substrates, and changing the coarseness or smoothness of a surface before coating.
It is widely used in the manufacturing industry, such as the automotive, rail, aviation, and shipbuilding sectors, where speed and volume play quite an important role.
The method is best performed in a blasting cabinet or booth and or with the help of special shot machines.
II. Bead blasting
In bead blasting, you’ll use glass bead abrasives to create smooth finishes through a predefined bead blasting process.
Often, operators will use glass beads to do general surface cleaning, where a uniform finish is required and the part is expected to have a dull “satin” finish.
III. Wheel blasting
In this type of blasting, no compressed air is used as the abrasive is propelled on the surface by a turbine that use wheels or strings with abrasive parts.
A blast wheel rotates and throws shot or angular grit toward the surface, cleaning off rust and removing other surface contaminants like mill scale, old coatings, and sand on foundry pieces.
This type of abrasive blasting is commonly used in manufacturing to speed up the cleaning process, eliminate cracking, and increase overall surface strength.
IV. Wet blasting
In wet blasting, a pressurized slurry (abrasives + water) is propelled onto the workpiece to process it. The presence of water means that there is more mass at the point of impact, resulting in some of the finest finishes.
Wet blasting is the way to go if you want to avoid any media particulates being embedded in the blasted surface. Due to the use of water, wet blasting reduces the amount of dust produced by the other types of dry abrasive blasting process.
This type of blasting is used in various industries to clean engines, prepare surfaces for painting, remove paint from surfaces, and restore stone or brick surfaces. It removes contaminants, corrosion, coatings, and residues from hard surfaces.
In Conclusion
Abrasive blasting has been in use for over a century now, and various blasting methods have been developed andemployed across industries with great benefits and success.
Choose the best abrasive blasting type based on your particular needs, making sure to pick the right equipment as well for best outcomes. Options for abrasive blasting types and abrasive blasting equipment are plenty.
Remember, before deploying this technique, equip yourself with adequate knowledge.